Every construction project begins with a simple question:how much will it cost?
Whether you’re working on a small home or a large building,you need a clear estimate to plan,budget,and avoid last-minute issues.
Cost estimation isn’t only about numbers. It’s about understanding the full scope—labor,materials,equipment,permits,and more.
This guide explains each part in plain terms. You’ll see why estimating matters,the types you’ll use,what details to include,and how to avoid common errors.
Common Challenges in Cost Estimation
Even experienced estimators face challenges when creating construction cost estimates. Some common challenges include:
1. Incomplete or Changing Designs
Often,designs are incomplete or change during the project. These changes can affect the accuracy of the estimate,requiring adjustments as the design is finalized.
2. Material Price Fluctuations
Material prices can fluctuate based on supply and demand. It’s essential to stay updated on the latest pricing and adjust estimates accordingly.
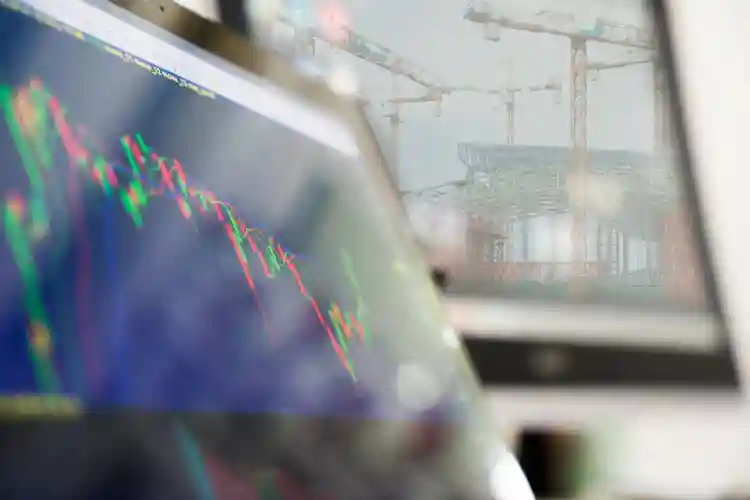
3. Unforeseen Site Conditions
Sometimes,site conditions are not fully understood at the time of the estimate. For example,the discovery of poor soil conditions may require additional foundation work,increasing costs.
4. Labor Shortages
A shortage of skilled labor can increase wages and lead to delays,which can affect the overall cost of the project.
Why Job Costing Software in Cost Accounting Will Be Your Next Big Obsession – Read More |
Key Components of a Construction Estimate
A construction cost estimatation is made up of several key components,each representing a different part of the overall cost structure. Here are the most important components:
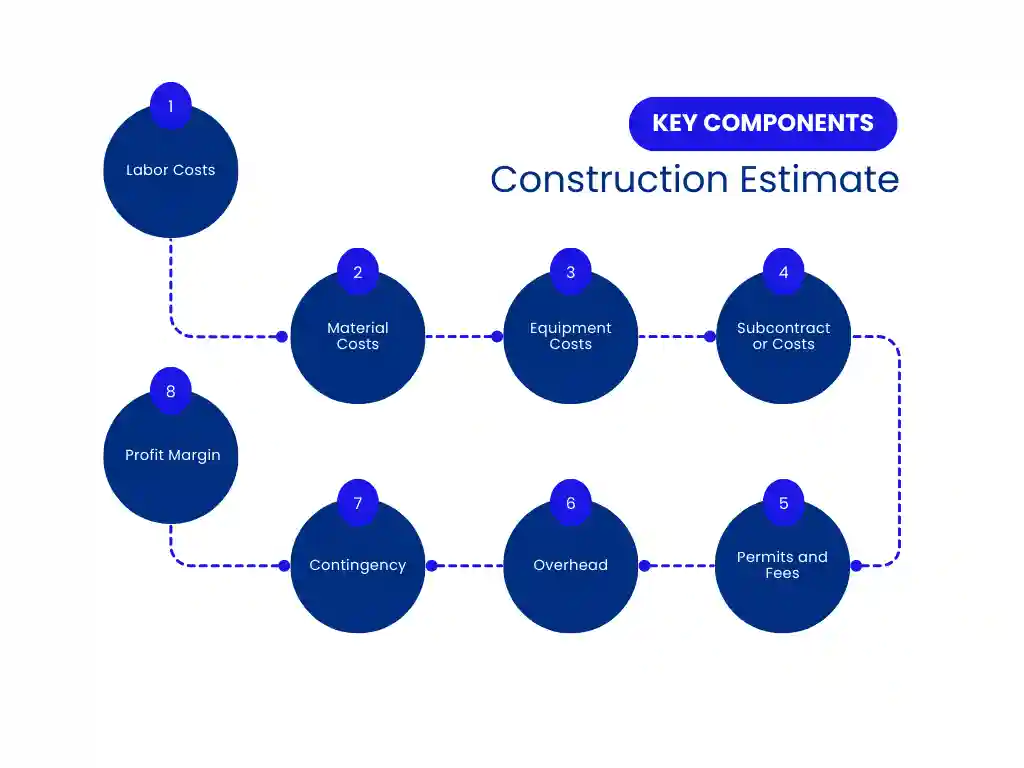
1. Labor Costs
Labor costs refer to the wages and benefits paid to the workers on the job site. The number of workers and the types of skills needed will vary based on the complexity of the project. It’s essential to account for the expected work hours for each worker and the potential for overtime.
2. Material Costs
Material costs represent the raw materials required for the project,such as concrete,steel,lumber,and other building materials. These costs can fluctuate depending on supply and demand,making it essential to stay updated on current prices.
3. Equipment Costs
Construction equipment costs include the purchase or rental costs for machinery used on-site,such as cranes,bulldozers,and excavators. The costs also involve the maintenance,operation,and transportation of this equipment.
4. Subcontractor Costs
Many construction projects rely on subcontractors to perform specialized tasks,such as electrical work,plumbing,or HVAC installation. These subcontractor fees are an essential part of the overall estimate.
5. Permits and Fees
Before construction can begin,the project must obtain the necessary permits from local authorities. These costs can vary significantly depending on the project’s location and type.
6. Overhead
Overhead costs refer to indirect costs that are not directly tied to the physical construction work. These can include project management fees,insurance,and office supplies.
7. Contingency
A contingency fund is a percentage of the total estimated cost,usually 5-10%,that is set aside for unexpected costs or scope changes. This is essential for dealing with unforeseen issues,such as unexpected site conditions.
8. Profit Margin
This is the contractor’s profit added to the overall estimate. The profit margin typically ranges from 5% to 20% and is included to ensure that the contractor can cover risks and still make a reasonable profit.
Construction Billing Methods Explained:Which One is Right for You? – Read More |
Steps in the Estimation Process
The construction cost estimation process involves several detailed steps:
1. Review Project Documents
Start by reviewing all available project documents,including architectural drawings,specifications,and other planning documents. This helps ensure that all necessary details are accounted for in the estimate.
2. Quantity Takeoff
This step involves measuring and quantifying the materials and components needed for the project. Accurate quantity takeoffs are essential for creating a reliable estimate.
3. Obtain Quotes
Once the quantities are determined,obtaining quotes from suppliers and subcontractors is the next step. These quotes provide the actual cost of materials,labor,and services required.
4. Calculate Labor Costs
Based on the quantity takeoff and project schedule,calculate the total labor costs,factoring in wages,work hours,and any specialized labor needed.
5. Add Overhead and Contingency
Next,overhead costs are added to the estimate,including things like insurance,utilities,and office expenses. A contingency is also factored in to account for unforeseen costs.
6. Final Review and Adjustments
Once the estimate is compiled,it’s reviewed for accuracy. Adjustments are made as necessary,ensuring that the final estimate is comprehensive and realistic.
Types of Construction Cost Estimation
Construction cost estimation change as the project moves forward. At the beginning,you only have basic details,so the estimate is rough. As you gather more information,you can create a clearer and more accurate estimate.
Here’s a closer look at the primary types of construction estimates:
1. Order of Magnitude Estimate
At the start of a project,when you only have basic details,you create a rough estimate called an “order of magnitude” estimate. You base it on past projects or early design ideas. This estimate gives a wide cost range and isn’t very accurate—usually off by 30% to 50%. You use it to see if the project idea makes sense.
2. Schematic Design Estimate
Once initial designs and plans are available,the schematic design estimate provides a more refined cost prediction. This estimate is based on architectural drawings and some design details,though it may still be subject to change. The accuracy improves,with a range of ±20% to ±30%. It’s a valuable tool for making initial decisions about materials and design modifications.
3. Design Development Estimate
As designs become more detailed and finalized,the design development estimate provides a higher degree of accuracy. This estimate uses precise quantities,material specifications,and labor rates. The accuracy at this stage is around ±10% to ±20%,making it highly reliable for project planning.
4. Construction Documents Estimate
This estimate is created when the project design is fully detailed,and construction documents are ready. The estimate is based on a comprehensive understanding of the materials,labor,and resources needed for the entire project. It is highly accurate,with a range of ±5% to ±10%,and forms the basis for contractor bidsand final budgets.
5. Bid Estimate
The final estimate is prepared by contractors when they submit their bids for the project. This estimate includes labor,materials,overhead,profit margin,and all other costs required to complete the project. Bid estimates are highly specific,and their accuracy is typically within ±5%.
How MetaConstructX Can Help
MetaConstructX helps with construction cost estimation by making the process easier and more organized. It gives up-to-date cost data,so teams can make better estimates. It also lets everyone work together in one place,which keeps the team on the same page.
The tool handles things like price updates and basic calculations,which saves time and reduces mistakes. It helps project managers see where money is going and plan better. With MetaConstructX,you can track costs and make smarter choices during the project.
Ready to take control of your construction costs? Try MetaConstructX todayand experience the future of project estimating.